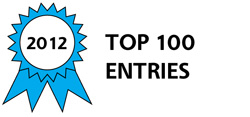
Bushing bearings are used as a cost effective alternative to much more expensive ball or roller bearings. The main drawback, however, is the radial clearance between the bearing and the shaft that continues to increase as the bearing wears. In addition to the noise generated, especially in a reciprocating motion application, there is a critical maximum clearance where the lubrication breaks down resulting in damage to the shaft as well as the bearing. The self-adjusting bushing bearing (SABB) design eliminates this failure mode and provides additional benefits that make it a more advantageous and cost effective alternative to ball, roller, as well as conventional bushing bearings.
Figures 1, 2, and 3 show an exploded view, partially assembled view, and assembled cross-sectioned view, respectively, of the SABB shown in a reciprocating linkage mechanism application. The figures shows that it consists of three bushing bearing segments continually “spring-loaded” against the bearing shaft by means of two O-rings wrapped around the OD of the bearing segments. Circumferential grooves around the OD of the bearing segments are used to position the O-rings. A retaining ring is used to retain the bearing segments in the bearing housing. The SABB design can replace bearing applications with cylindrical shafts using cylindrical ID SABB segments rather than the spherical ID segments shown.
The SABB has the following advantages with respect to standard bushing, ball, and roller bearings:
1.While there is a slight increase in the cost of the O-rings with respect to standard bushing bearings, it is still significantly less expensive than ball or roller bearings.
2.There is no need for any type of press fit to secure the bearing to the housing to prevent the bearing from spinning relative to the housing, reducing machining tolerances and costs and making it much easier to replace in the field.
3.The gap between the bearing segments functions as a wear indicator for preventative maintenance to prevent the shaft from being damaged.
4.The constant “zero clearance” between the bearing segments and the shaft helps prevent contaminant (dirt, water, etc) from entering between the bearing and the shaft resulting in less susceptibility to contamination without seals or with bearing seals if/when they fail. Note: when used with sintered bushing bearing material, any dirt particle that is small enough to migrate into the essentially “zero clearance” oil boundary layer will be small enough to pass into the sintered bearing material void space rather than become trapped between the bearing material and shaft.
5.The O-ring spring loading between the bearing segments and the bearing housing also provides:
•Additional tolerance for misalignment
•Vibration dampening to assist in passing through any natural frequencies (such as during startup)
•Shock absorption
6.The “zero clearance” design accommodates the use of much less viscous (relative to oil) lubricants such as water for applications such as boat propeller shaft bearings.
-
Awards
-
2012 Top 100 Entries
Like this entry?
-
About the Entrant
- Name:Douglas Larson
- Type of entry:teamTeam members:Tom Danowski
Doug Larson - Software used for this entry:Solid Works
- Patent status:pending