2012
Transportation
Emerging electric vehicles require high starting torque smooth running high power tracking motors. Developing such motors is a technological challenge.
Currently, hybrid and electric vehicle use motors with rare-earth permanent magnets in the rotor. This eliminates providing current to the rotor which eliminates power loss, and decreases maintenance.
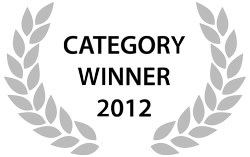
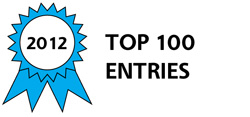
I propose a new approach to implementing vehicular Tire Pressure Monitoring Systems (TPMS) which is more economical and ecological than existing systems mass-deployed in the market to date, with significant advantages, the foremost being the passive non-electronic sending unit (inside the tire) thereby eliminating RF electronics, thermal compensation issues,
In the process of internal combustion locomotion for most of the energy of the fuel is dissipated into heat energy.
The idea is to provide a radiator effect seebek that recovers part of the thermal energy dispersed into electrical energy to be conveyed, for example in hybrid vehicles, locomotion.
The main idea is to create some waiting file at low speed for cars when it is anticipated that they will have to stop in front of a red light.
There is a green wave where cars drive at high speed (within speed limit) where it is anticipated that the green wave will go through the green light.
Electric car efficiency can be improved. Current designs use transmissions and differentials. Improved motor design with lower loss allows direct drive without transmissions and differentials. Cost and complexity are reduced and performance is increased.
I propose the use of automobile tire grindings as an economical and eco-friendly additive to hybrid rocket motors. To bind the granules, I also propose the use of a low-viscosity,
Rotary-Hybrid Engine
FACT:
The monopoly of using all known internal combustion engines (ICE) has only reciprocators on the ground and gas-turbines (GTE) in the air.
PROBLEM:
Reciprocator’s drawback is high demand on properties and quality of fuel.
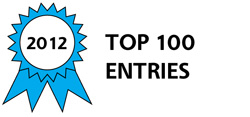
Imagine for a moment, a reasonably priced automobile with 5 or even 11 different sized engines in it, one for every driving situation from creeping along in traffic to safely towing a large boat or travel trailer up a mountain.
The future of air transportation is all about protecting the environment and responding to increasing energy costs in a balanced way. In the future, we will need airplanes that are quieter and more fuel efficient and we need to introduce these new technologies without impairing the convenience, safety and security of commercial air transportation.
Walking Mechanical Mule
The Walking Mechanical Mule is a very simple, purely mechanical walking platform. It is based on a special form of unique "7 link mechanism." It is actuated by a simple rotating crank and it has NO additional controls!
The Walking Mechanical Mule presented here was built as a "Proof of Principle" prototype and extensively tested.
Page 9 of 14